The 8th edition of the Hyundai Great India Drive saw us take the ALCAZAR deep into the heart of Gujarat to rediscover the true meaning of slow fashion.
Everything you need to know about the Hyundai Great India Drive is right in its name. It’s that time of year when we jump into one of Hyundai’s many excellent cars and head off on an adventure to learn more about what makes our country so wonderful. In past years, we’ve covered everything from our regal tigers to the mighty Himalayas to our beautiful beaches, and more. This time around, though, we’re choosing to focus on something different.
Leg 1 of this year’s Hyundai Great India Drive was flagged off at the extremely picturesque Rann of Kutch.
Cotton. It’s a fabric so common, so everyday, that we hardly ever stop to think about where it comes from or how it’s made. But deep within the heart of Gujarat, there exists a version of cotton so pure, so untouched by modern machinery, that it carries the very essence of sustainability. With the entry of mass-market fashion brands and the advent of fast fashion, people seem to have forgotten our nation’s rich tradition of crafting sustainable, eco-friendly textiles. But a few determined brands have made it their mission to help these traditions survive, and this story revolves around two such brands – House of Miko and House of Idar, jointly run by Avisa Keskar Dastur and Trushal Shah. To track down the full story, we embark on an adventure that takes us across the state to rediscover the meaning of slow fashion. And by our side on this incredible journey, the Hyundai ALCAZAR, our trusty companion as we traverse remote landscapes, uncovering an age-old craft in a modern world.
The first order of business is making our way towards Bhuj, which means mile after mile of long, straight highway shooting off into the distance ahead. The 1.5-litre turbo-diesel engine quite happily stretches its legs out on the open road, quickly settling into a brisk cruise with the motor purring away under the hood. And with the well-balanced suspension setup keeping everything steady, the miles quickly tick by, and before we know it, we’re surrounded by the vast open expanses of Bhuj. And right into the thick of the action at the Khamir Craft Resource Centre.
This is where we speak to Mr Paresh Mangalia about what makes the cotton in these parts so special. And what we learn is that the soft staple cotton that’s native to this region, the one that goes by the name Kala Cotton, is one of the most resilient and sustainable types of cotton in the world. It requires no irrigation, fertilisers or pesticides to cultivate, making it a crop that’s organic by nature, and one that can survive even in the arid semi-desert climate of Bhuj with very little rainfall. But it isn’tjust the sort of cotton or the way it’s grown that can make a garment sustainable; it’s also about the way it’s dyed.
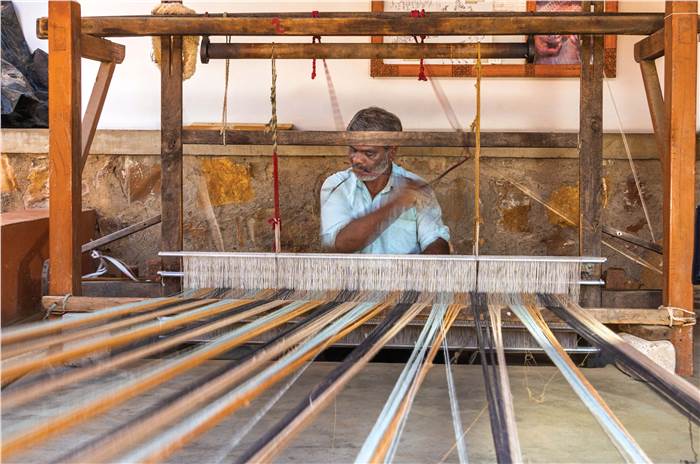
And to find out more about that, we shift our attention to a craft that dates back thousands of years and yet still remains surrounded by an air of mystery: indigo dyeing. At the Vikram Vankar Valji centre in Bhujodi, the deep blue hues emerge not from chemicals but from nature itself. Dinesh Vikram Vankar devoted 15 long years of his life to mastering the art of indigo dyeing, to the point where he became almost possessed by it.
Speaking to him sat by the 11 indigo vats he’s been responsible for creating, the passion is tangible. “These vats are like little children, they have their own moods. Some days they colour wonderfully, other days not so much. You have to really care for them, make sure they’re getting everything they need, and cure them when they happen to fall ill,” he explains with a tenderness in his voice. It’s a process that’s not quite as straightforward as easygoing elocution would have you believe. Caring for these vats isn’t just as simple as adding the indigo pigment and throwing in the yarn – the dye needs to be fermented, at the right acidity level and temperature, and even with everything in place, each vat can only dye about 300 grams of yarn per day, and it all happens in the top 1 foot of the 3-foot-deep container. The middle portion is still in the process of fermentation, and the bottom contains the various solid additives, which include everything from a paste made from dates to aid fermentation, to lime for controlling acidity, and the indigo pigment itself.
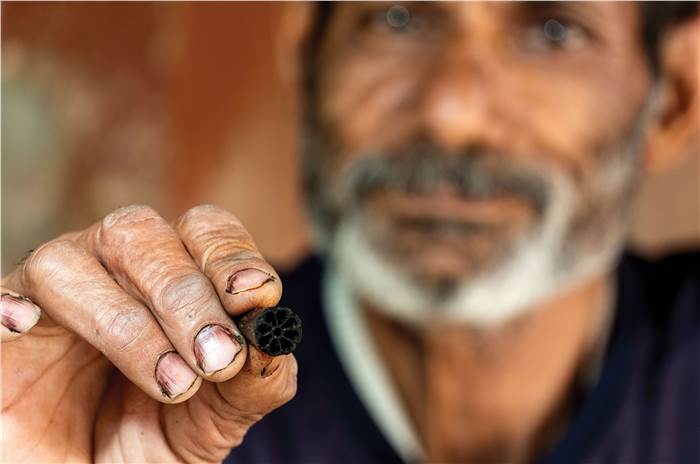
Mansukhbhai’s patience is evident as he patterns an entire bedsheet using just this tiny block.
Just a stone’s throw away from where Dinesh plies his trade, you’ll find the town of Ajrakhpur, where the Khatri family has been involved in the art of Ajrakh printing since the 15th century. Once again, there’s more than meets the eye, with the process from plain white textile to finished fabric taking 16 days. The format itself is ancient – a type of resist printing where you block out the sections that don’t need colouring with gum and some lime, before dyeing the rest of the fabric in the colour you want, and then finally block printing the desired pattern. But Sufiyan Khatri, a 10th-generation Ajrakh artisan, has been putting his own modern spin on things. “After COVID, I started working on some fresh designs. I have a passion for trying new things, I try to wake up every morning and try something different. It excites me to progress further, while also supporting the community of artisans that work with me,” he tells us with a glint in his eye.
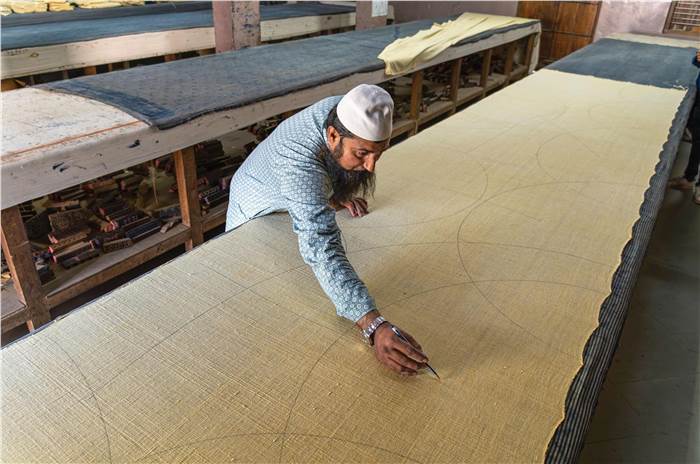
Sufiyan Khatri sketches designs free-hand on fabric – something his family has been doing in Ajrakhpur since the 15th century.
It’s now time to leave behind the wide open landscapes of Bhuj for a town that seems to have stood still in time. With the ALCAZAR’s plush cabin keeping us nice and cosy despite the sweltering heat outside, we roll into the old-world town of Gondal. Here you’ll find no machines whirring away; instead, just the steady rhythms of manual looms, and devoted craftsmen and women painstakingly operating them to weave fabric the old fashioned way – by hand. Here at Udyog Bharti, where generations have dedicated their lives to keeping the ancient craft of Khadi alive, Khadi isn’t just fabric, it’s a movement. Kavin Patel explains, “Khadi is a fabric that is hand spun and hand woven. But more than that, Khadi has always been a symbol of self-reliance. Similarly, Udyog Bharti is also an institution that focuses on empowering people by engaging them in Khadi activities. What we’ve been trying to do with Khadi is give it a modern touch, so it becomes appealing to young people and the craft can sustain itself.”
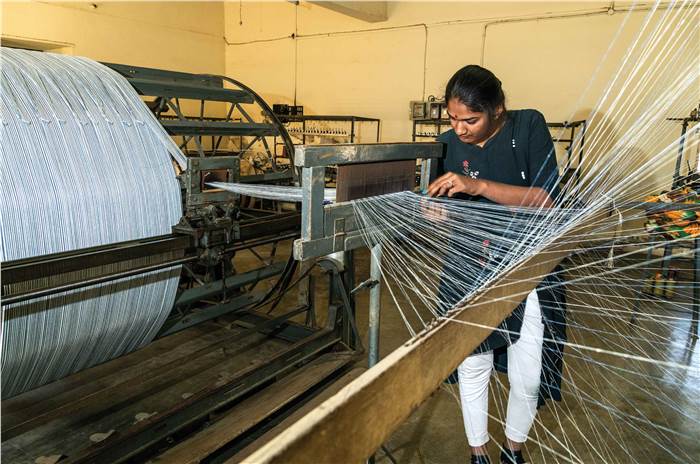
At Udyog Bharti in Gondal, you’ll hear no machines. Just the steady rhythm of manual looms.
Raw cotton, woven by hand and dyed with natural pigments. We now have all the ingredients we need. But here is where sustainability meets design. Our final stop takes us to the town of Himatnagar, home to the manufacturing facility where the raw beauty of Khadi, Kala Cotton and Indigo is shaped into silhouettes that are timeless, thoughtful and truly one of a kind. This is a process that believes in quality over quantity. But, more importantly, this is fashion that is conscious, not wasteful. Standing here, surrounded by pieces that tell stories steeped in a rich history, we realise that we’re not just looking at clothing. We’re looking at a movement, one that redefines what sustainable fashion can be. As it turns out, the future of fashion isn’t just about what we wear. It’s about how it’s made. And here, in the heart of Gujarat, the future is already being woven.
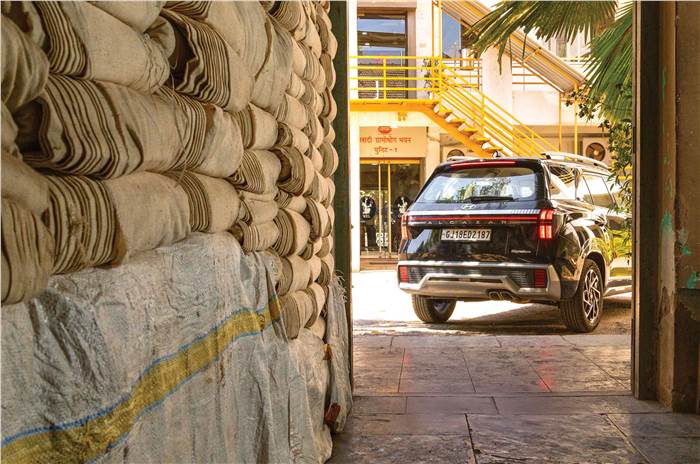